Extruded plastics are cooled in a variety of strategies—by water, air, and chill rolls. Chill-roll cooling has primarily probably the most merely definable cooling calculation, nonetheless I nonetheless see considerable ambiguity as regards to the selection of roll stacks for sheet.
For sheet extrusion it’s widespread to have some geometric variation of a three-roll vertical stack, with most likely some further rolls for very high-speed strains the place the contact time is transient. In sheet, the best roll has solely a minor cooling impression because of the polymer has a small contact area.
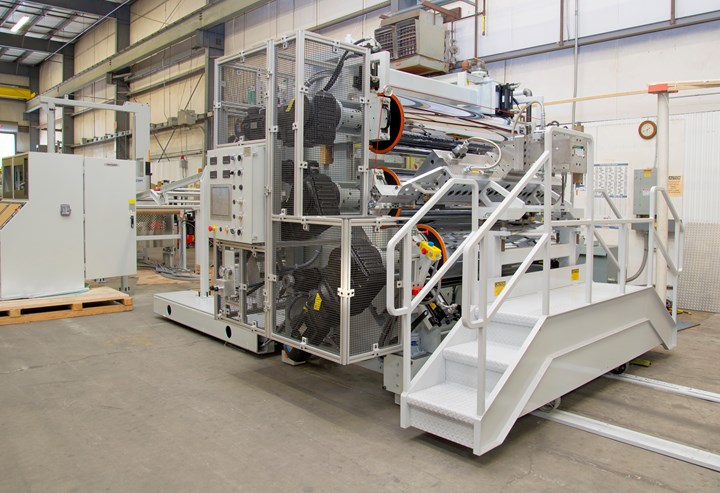
J-Stack designs like this one are typically used for PET, PETG, PS, and PP. ({Photograph}: Davis-Regular)
There are 4 main points to ponder in deciding on the precise stack to your software program: the overall cooling functionality, the merchandise to be processed, the mechanical performance, and the rolls’ inside design. Considering merely the cooling functionality, the best roll is there to set the sheet thickness along with its uniformity. Generally, decrease than 10% of the roll is in contact with the plastic, minimizing the realm for heat change. The middle roll does lots of the cooling because of it has about half its circumference coated with the polymer and the plastic is hottest there, maximizing the heat change to the cooled roll. The third roll moreover has 50% or further of its circumference in contact with the plastic, nonetheless since a complete lot of the heat inside the plastic went into the middle roll the heat-transfer cost is often quite a bit a lot much less for the third roll. Nonetheless, as a result of the third roll cools the opposite side of the sheet from the middle roll, it turns into extra sensible for thicker sheets. It takes time for heat to maneuver by the use of the sheet, and the thicker the sheet the lower the share extracted on one express roll.
There are pretty a few considerations for the proper roll sizing, based totally merely on the completely totally different polymer properties. That is, there is no frequent roll set. The roll’s cooling effectiveness varies with the form of polymer, the roll design and the coolant. I will stick with the polymer variations on this text, as they’ve a serious impression on the cooling. The heat-transfer cost, explicit heat and soften temperature are a very powerful determinants of the cooling cost.
Let’s take note of a line processing HIPS in distinction with one processing HDPE, with every having the similar soften temperature of 375 F and a desired exit temperature of 120 F. So 375-120 = 255° F cooling in every circumstances, nonetheless while you multiply that by the actual heat of the polymer, the outcomes are pretty completely totally different.
HIPS: 255 F × 0.32 BTU/lb-°F = 81.6 BTU/lb
HDPE 255 F × 0.55 BTU/lb-°F = 140.3 BTU/lb
There could also be 72% further heat to be away from the HDPE on the same output cost (lb/hr). Nonetheless, the pace of heat change in HDPE is bigger than double that of HIPS. So regardless that there is further heat to be transferred with the HDPE, it strikes by the use of the sheet higher than twice as fast from the polymer to the roll flooring. Whereas which means it’s doable cool these two polymers at associated prices, the HDPE would require further coolant circulation for that to happen.
Now let’s consider HDPE with PP:
PP: 255 F × 0.52 BTU/lb-°F = 132.6 BTU/lb
HDPE: 255 F × 0.55 BTU/lb-°F = 140.3 BTU/lb
They’re very shut in heat content material materials (0.55 vs. 0.52 BTU/lb-°F) nonetheless the heat change cost of PP is 60% of that of HDPE (0.15 vs. 0.09 BTU/Ft-Hr-°F). That signifies that beneath the similar circumstances of output, roll temperature and soften temperature, it could take 60% further time on the rolls to accumulate the similar exit temperature for the PP as a result of the HDPE.
Together with these properties, the soften density comes into play when the comparisons are based totally on kilos per hour. Inside the case of HIPS vs. HDPE, the HIPS soften is 33% further dense, so that the heat has a shorter distance to journey, eliminating half the profit in heat-transfer cost for HDPE. Inside the PP/HDPE comparability, the PP has a barely lower soften density than the HDPE, so that the heat has a barely higher distance to journey, worsening the comparability.
Heat-transfer cost, explicit heat and soften temperature are a very powerful determinants of the cooling cost.
The aim of this dialogue is that there is no “frequent” roll cooling instruments because of the variations inside the polymer thermal properties. Even the soften density of the polymer impacts the effectiveness of the roll cooling due to the variations in heat-transfer cost. When the polymer thermal properties are coupled with the mechanical requirements, the roll design/measurement and the roll cooling system, the selection of the roll stack turns into pretty a fancy concern.
That’s notably important in foreign-made or used instruments, the place a knowledgeable OEM’s expertise is not going to be accessible. Be sure that when looking for new or used instruments that any individual can think about the roll cooling to your exact software program(s).
ABOUT THE AUTHOR: Jim Frankland is a mechanical engineer who has been involved in all types of extrusion processing for higher than 50 years. He is now president of Frankland Plastics Consulting, LLC. Contact jim.frankland@comcast.web or (724)651-9196.